A truck waits to offload its cargo at Phnom Penh Port. Prime Minister Hun Sen warned the logistics industry Monday that illegal practices would lead to company closures.
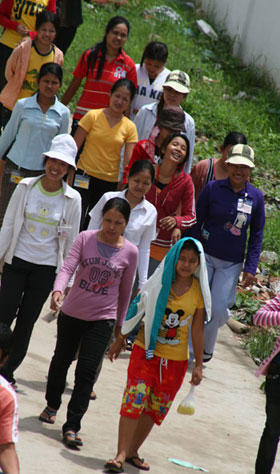
14-productivity.jpg
Everyone agrees that increased productivity is crucial to a thriving Cambodian garment industry, but neither private companies nor the government are rushing to train workers in the ailing sector upon which the nation’s manufacturing economy is based. Brendan Brady and Meas Sokchea look into how deep the problem runs and what needs to be done.
TRACEY SHELTON
Garment workers leave a factory in Phnom Penh’s Dangkor district at the end of their shift on May 14. Most Cambodian garment factories operate at 30-40 percent efficiency, far below the desired 70 percent, according to the Garment Manufacturers Association of Cambodia, which says companies should assume most of the responsibility for raising productivity levels.
A
A threatened nationwide strike in Cambodia’s garment sector was narrowly averted last month when manufacturers agreed to provide workers with an additional $6 a month to supplement their incomes amid spiraling food costs.
But many see the small increase as merely a short-term solution that fails to address the workers’ underlying concerns over fair wages and factory conditions, and warn that future disruptions only highlight one of this key sector’s most serious problems: poor productivity.
As Cambodia’s multibillion-dollar garment sector, which is the country’s largest single source of foreign exchange, faces stiffer competition from its neighbors, particularly Vietnam and China, unions and factory owners alike are going to have to find ways to boost output or risk being swept aside, industry monitors and officials say.
“If Cambodia is to keep its garment industry and eventually diversify its manufacturing base, it must increase productivity and make workforce development a higher national priority,” said Erin Soto, mission director of USAID.
Most Cambodian factories are operating at 30 to 40 percent efficiency, far below the desired 70 percent, according to Kaing Monika, external affairs manager of the Garment Manufacturers Association of Cambodia (GMAC), an organization of industry executives.
“Efficiency and productivity is our concern,” Monika told the Post by email. “Compared to [other] countries in the region, we are less productive.”
A fortunate beginning
Cambodia’s garment sector in the past has enjoyed immunity from its competitors through preferential trade deals and restrictive quotas on other countries’ sectors, most notably that of regional powerhouse China.
The country has also fostered, with the help of monitors like the International Labor Organization (ILO), a reputation for clean working conditions, allowing it to avoid the “sweatshop” label and carve out a unique niche among international garment retailers.
If Cambodia is to keep its garment industry … it must increase productivity and make workforce development a higher national priority.
But sector safeguards are set to expire soon – China will have access to US markets at the end of 2008 for products that are also produced by Cambodia – and goodwill over fair labor practices alone cannot prop up Cambodia’s garment industry, one official said.
“Cambodia’s garment industry has very high standards, even world-class, for working conditions and this is valued by international buyers,” said Tep Mona, director of the USAID-sponsored Garment Industry Productivity Center (GIPC), which was established in 2005.
“However, without competitive costs, reliable quality and on-time delivery, the buyers will look to other countries,” Mona said.
For an industry that employs as many as 350,000 people – mostly poor young women supporting families in the countryside – collapse would be disastrous for an economy that is only just beginning to recover after decades of civil turmoil.
Already, the sector is showing signs of strain. Exports, which enjoyed annual growth of around 20 percent during the past five years, plummeted by nearly half in the fourth quarter of 2007.
While this was partially due to decreased demand amid a global economic slowdown – particularly from the United States, Cambodia’s largest garment importer – it was also a sign that garment workers need to keep pace with their counterparts in other regional manufacturing giants.
But the problem still lies in the fact that the largely unskilled workforce that makes up the bulk of the industry has few avenues to improve its skills, according to Tuomo Poutiainen, chief technical advisor of the ILO’s Better Factories program.
“What little training exists in Cambodia focuses on improving factory systems,” he said.
“There aren’t any public vocational schools and the few private ones are limited and cannot provide what the industry needs: a higher skilled work force.”
‘Factories most responsible’
Another complication is disagreement over who should better train workers, said officials.
Foreign factory owners are unlikely to invest in training, seeing their Cambodian properties as limited assets in a larger global portfolio, said the GIPC’s Mona.
The ILO offers short courses in productivity, and while GMAC does provide supervisory training for small groups of workers, it does not offer any in-factory instruction.
“The factories themselves are most responsible for providing training to workers by way of on-the-job training,” said GMAC’s Monika.
This, however, is rarely done, according to labor union leaders who say factory management has shown little interest in improving the skills of their workforce.
“If they want to provide skills training to workers they should invite the [Free Trade Union] or a worker representative, but they never have,” said Chea Mony, president of the FTU, Cambodia’s largest trade union, dismissing such initiatives as cosmetic.
But better training, as well as better incentives to work like productivity bonuses could go a long way in making Cambodia competitive with its neighbors – as well as result in higher salaries for workers, officials say.
“You add to a workers’ training and it makes it easier for them to find jobs, and higher paying ones. Productivity pays off, it’s not exploitative. It’s good for workers, for manufacturers, and for the country,” said Poutiainen.
“Everybody knows about productivity but there haven’t been concrete measures to move forward on it.”
Contact PhnomPenh Post for full article
Post Media Co LtdThe Elements Condominium, Level 7
Hun Sen Boulevard
Phum Tuol Roka III
Sangkat Chak Angre Krom, Khan Meanchey
12353 Phnom Penh
Cambodia
Telegram: 092 555 741
Email: [email protected]